What to Know
- Answering a hospital's call to donate masks, gloves and protective eyewear, exhibit developers at the Exploratorium realized they had the tools to build tailor-made safety equipment from scratch
- The prototype face shields and other PPE evolved into open-source designs distributed under the name Something Labs, and also manufactured at small plants throughout the Bay
- Maker Nexus, a non-profit maker space in Sunnyvale, worked with South Bay hospitals to create a different set of open-source designs that are easily laser cut and 3D printed by volunteers
Sam Haynor had finally landed his dream job.
After visiting the Exploratorium for the first time when he was 9 years old, he fell in love with the museum's hands-on way of teaching kids about science.
"The first time that a job came up here in my adult life, I applied for it and got very lucky," he said.
The Exploratorium's way of designing exhibits has a lot in common with what Silicon Valley hardware makers know as "rapid prototyping."
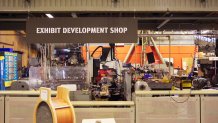
"The whole idea is to make things as quickly as possible, and then get them out, get them broken, get them messed with, futzed with, and try to learn from the ideas that come out," Haynor said.
Local
That method — and the tools that go along with it — turned out to be invaluable as the rapid spread of COVID-19 began to create a global shortage of personal protective equipment in hospitals.
"I think in moments of crisis, you just look at whatever you have around you, and see if you can apply it in any way," Haynor said. "It kind of began with the shop unanimously voting to donate every last thing that we had here at the museum. And when that was done, and we'd cleared that all out, it was obvious that that wasn't enough. But we have a shop, we have engineers, and we have materials. and so it began there."
Get a weekly recap of the latest San Francisco Bay Area housing news. >Sign up for NBC Bay Area’s Housing Deconstructed newsletter.
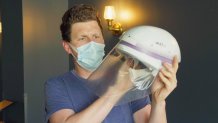
Both shocked and inspired by images he'd seen of hospital workers using makeshift face shields built from office supplies, Haynor decided that prototyping a proper face shield would be a good starting point.
"Basically, suspending a piece of plastic in front of your face," he said. "If you can do that reliably and comfortably, then you've made a successful face shield."
Using the Exploratorium's laser cutter and CNC router, Haynor and the other engineers in the exhibit shop began cutting brims, fasteners and clear lenses out of leftover plastic until they arrived at what felt like a final design — then shared the specifications and 3D computer files with a network of volunteers. Just like many popular software programs that are continuously being improved by the developer community, these designs are open-source.
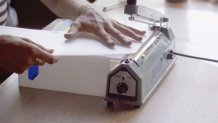
"Open-source allows us to work with other people very, very quickly, and it falls into the idea that the Exploratorium has, which is to share ideas wherever possible," Haynor said. "To compare notes, and motivate, and shift to whatever's working."
Open-source design is a core part of what became known as the "maker movement," a flurry of excitement around building physical things using new high-tech tools like 3D printers. The movement flourished in the early-to-mid-2010s, then fell on hard times with the closure of maker space chain TechShop and the shutdown of Make Magazine and the Bay Area's flagship Maker Faire event.
But the leaders of Maker Nexus, a new non-profit maker space in Sunnyvale, assure us the movement is far from over. In fact, they say the COVID-19 pandemic is giving some makers a new mission.
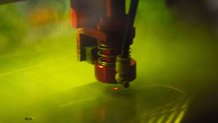
"We got a tweet from one of the local medical centers, Valley Medical Center Foundation, that they were in desperate need of any type of PPE, personal protective equipment," said Eric Hess, the general manager of Maker Nexus. "We had a few N95 face masks available, we donated those, and we didn't have any face shields available, but we did have a laser cutter and a bunch of 3D printers."
Using an open-source design from the Czech Republic as a starting point, Maker Nexus members enlisted the help of doctors at Santa Clara's Kaiser Permanente hospital to rapidly iterate on the design over the course of four days. The goal was to create a face shield that would earn the hospital's seal of approval, and could be easily 3D printed and laser cut.
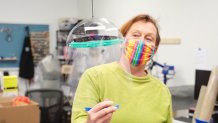
The final design, while funny-looking, passes that test with flying colors. It's a clear plastic lens shaped like a hand with floppy fingers, attached by small pegs to a colorful headband. The "fingers" are joined together at the top with a single zip tie, forming a half-dome to protect the wearer's head from coughs and sneezes.
"It's not FDA-approved, but it's hospital-approved, doctor-approved," said Maker Nexus executive director Regina Sakols. "And some doctors mention this is the best they've ever had."
With hundreds of volunteers 3D printing headbands at home, and Maker Nexus employees cranking out lenses on the laser cutter, the design was tweaked and finalized before beginning a transition to injection-molded plastic headbands. An East Bay factory donated a mold for the final headband design — ordinarily an investment of $15,000 or more, Hess said.

"3D printing, as remarkable as it, is is a very time-consuming process," he said. "Injection molding ... produces thousands of parts per day."
The Exploratorium team also quickly pivoted its efforts into higher-volume manufacturing techniques — relying on a network of small shops in the East Bay that produce different parts using different kinds of cutting tools, from a die press to a CNC oscillating knife. This "distributed manufacturing" approach finds Haynor serving as driver-in-chief, delivering huge rolls of donated plastic and ferrying finished parts back to a newly-established assembly plant in an Oakland office building.
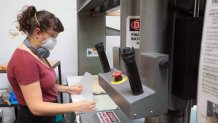
"The things that I've done for plastic have been absurd," Haynor said. "Every week, it changes. Every week, I think I have a reliable source, and every week, we've shifted."
And yet, he said, he's inspired by the generosity he's seen — both from companies donating materials and individuals donating their time.
Volunteer Brian Shire, who's been making face shield headbands and intubation boxes in his spacious home workshop, explained his eagerness to help out:
"If I ended up in the hospital and looked up at my doctor friend working on me, it'd be nice to know they had what they needed to do their job properly and feel safe," Shire said.
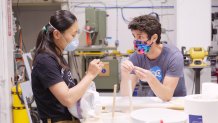
Hanyor said the Exploratorium has been supportive of the team's effort, but as it continues to grow, the new grassroots organization needs its own identity.
"We have to come up with something, and well, we have to do something," he recalled musing at the time, before settling on the new name: Something Labs.
He said he can't wait to get back to designing exhibits — but he also knows the PPE shortage isn't going away overnight, and he's here to see it through.
"The very first thing I said is that this is gonna go on until we were no longer useful, or until I ran out of money," he said. "I ran out of money three times, and we're still going."